Булат (металл) — Википедия
Материал из Википедии — свободной энциклопедии
Текущая версия страницы пока не проверялась опытными участниками и может значительно отличаться от версии, проверенной 1 июня 2017; проверки требуют 29 правок. Текущая версия страницы пока не проверялась опытными участниками и может значительно отличаться от версии, проверенной 1 июня 2017; проверки требуют 29 правок. Клинок ножа из булатной стали У этого термина существуют и другие значения, см. Булат.Була́т (от авестийского «chmolohikus», ср.-перс. «pulad» — «сталь») — сталь, благодаря особой технологии изготовления отличающаяся своеобразной внутренней структурой и видом («узором») поверхности, высокой твёрдостью и упругостью.
С древнейших времён (первые упоминания встречаются ещё у Аристотеля) используется для изготовления холодного оружия — клинков мечей, сабель, кинжалов, ножей и других.
Булат производили в Индии (под названием вуц), в Средней Азии и в Иране под названиями
ru.wikipedia.org
Открытие секрета булата
Pаботы Аносова создали новую технику, новые методы производства качественной, «совершенной стали».
При «отыскивании тайны приготовления булатов» Аносовым были разработаны четыре метода производства качественной стали главным образом за счет усовершенствования тигельной плавки.
Первый метод — «сплавление железных руд с графитом, или восстановление и соединение железа с углеродом»93, то есть метод непосредственного восстановления железа из руды. Этот способ Аносов и считал подлинным методом производства булатов на Востоке. «Древние,— говорил он,— скорее могли напасть на способ простой, нежели сложный» благодаря тому, что «употребление тиглей столь же древне, как и известность золота; ничего не могло быть ближе для древних алхимиков, как испытание плавкою всех тел, похожих по наружному виду на металл»94.
Однако этот метод не мог удовлетворить Аносова. Для применения метода были нужны чистейшие руды, не содержащие посторонних примесей, особенно серы. Кроме того, он был невыгоден экономически. «Дороговизна делает сей способ недоступным для введения в большом виде»,— замечает Аносов.
Разработка этого метода, раскрывая секрет производства булатной стали, в то же время не отвечала общей задаче, поставленной исследователем,— массовому производству качественной стали. Поэтому Аносов продолжал изыскания, стремясь найти метод, более приемлемый.
Второй метод — «сплавление железа при доступе углей или соединение его предварительно с углеродом и восстановление его посредством закиси железа» (то-есть переплавка чугуна с окалиной)
Этот способ также оказался непригодным для массового производства стали. Получаемый металл содержал много углерода и с трудом подвергался ковке. По мнению Аносова, это происходило оттого, что круглое железо было недостаточно чистым, плохо очищалось при тигельной плавке.
Открыв второй метод, Аносов положил им начало процессу передела чугуна в сталь, широко известному теперь под названием скрап-процесса, намного опередив французов братьев Мартен.
Второй метод также не был использован Аносовым, но впоследствии оказался полезным известному новатору
Фиг. 12. Отрывок из труда П. П. Аносова «О булатах» о преимуществе златоустовской стали перед английской.
русской техники инженеру А. А. Износкову, который, используя его, сумел в 1869 г. сравнительно легко и быстро организовать передел чугуна в сталь в первой мартеновской печи в России, на Сормовском заводе.
Третий метод — получение литого булата (сталь отливалась в форму) при продолжительном отжиге без доступа ©оздуха (в засыпке). Этот способ был использован Аносовым на Златоустовском заводе для получения литых булатов, «годных на выделку дешевых изделий».
Сущность метода состояла в том, что стали, приготовленной в тигле, не давали °атвердевать в тигле, а отливали ее в формы. «Отливка стали в форму,— писал Аносов,— хотя нарушает наклонность к кристаллованию (то есть создает иные условия кристаллизации, чем при застывании большого ее количества в тигле), но она необходима для облегчения проковки больших сплавок и составляет единственное средство к удешевлению булатов до ценности стали.
Литая сталь подвергалась длительному отжигу в специальной печи, сконструированной Аносовым, без доступа воздуха, будучи тщательно закупоренной в ящике. Преимущество отожженной стали заключалось в том, что она «удобно куется, мягче в опиловке, менее повреждается в закалке и стойчее после оной». На отожженной стали обнаруживались узоры: на мягкой — мелкие, на твердой -крупные. Чем лучше было качество стали, тем скорее она приобретала крупнозернистое строение. «Отожженная сталь, как имеющая узоры, подобные булатным, должна нести и одинаковое с ней название. Для отличия от настоящего булата я называю ее литым булатом»,— говорил Аносов.
При определении технологии отжига Аносов обратил внимание на различный характер изменения свойств стали. Неправильный отжиг, связанный с доступом воздуха в коробку, вызывал обезуглероживание поверхности, характерное «зернистым сложением на поверхности», которое создавало «особый кант белого цвета по -краям бруска». Пережог брусков («повреждение стали») характеризовался «удобным разламыванием их без закалки». Хорошо отожженная сталь имела чистую поверхность без следов окалины, хорошую вязкость и «ровное крупнозернистое сложение в изломе».
По наблюдениям Аносова, части, соответствующие верху отлитой болванки, «почти никогда не имели крупнозернистого строения, а следовательно, и узора — рисунка. Это обстоятельство позволило Аносову сделать заключение, что ясность узора связана не только с кристаллическим строением, но и с чистотой стали. Аносов широко использовал отжиг не только на литых сталях, но и как предварительную операцию, отжигая сталь, идущую в шихту.
Применение отжига значительно повысило качество златоустовской стали, поставило ее выше лучшей английской тигельной стали. К тому же найденный Аносовым способ получения качественной стали был «много проще английского. «Подобного улучшения не было достигнуто в Англии помощью отжигания,— писал Аносов,— мне кажется потому, что тамошние мастера недовольно обращали внимание на изменения в стали при различных условиях отжигания, а приписывали улучшение ее более влиянию посторонних тел, -при отжигании обыкновенно применяемых».
Здесь Аносов также поднимается выше своих современников — иностранных ученых, отдавая должное превращениям в самой стали, а не внешним факторам, например, влиянию засыпки и ее «магическому» действию.
Ироническое отношение Аносова к качеству английской стали и устаревшему с его точки зрения способу Гэнстмана — методу тигельной переплавки предварительно цементованной стали, очень хорошо выражено им в следующих словах: «Бритва из хорошего булата, без ошибок приготовленная, выбреет, по крайней мере, вдвое больше бород, нежели лучшая английская».
Четвертый метод — «сплавление железа «непосредственно с графитом, или соединение его прямо с углеродом»101 — Аносов считал наилучшим из всех разработанных им и экономически наиболее выгодным «к получений) настоящих булатов».
Эту точку зрения разделяли и русские ученые. Один из современников Аносова — проф. П. П. Эйнбродт,— восхищенный его трудом «О булатах», в личном письме к нему подчеркивал значение четвертого способа, заявляя, что им исследователь «справедливо может гордиться».
Для четвертого метода Аносов разработал полную технологию. Эту интересную технологию мы приводим в сокращенном виде.
Плавка. В тигель загружали 12 фунтов (около 5 кг железа). Если же необходимо было получить более твердый металл, количество железа уменьшалось до 10 или 8 фунтов. Железо засыпалось смесью графита, железной окалины и флюса. В качестве флюса Аносов рекомендовал доломит.
После загрузки тигля его закрывали глиняной крышкой и пускали дутье для достижения «сильного жара». Дутье регулировалось «ртутным духомером». По истечении трех с половиной часов металл расплавлялся и покрывался тонким слоем шлака с плавающим в нем графитом, всплывшим частично в шлак.
Потери графита составляли за этот промежуток времени 100 г. После плавки в течение четырех с половиной часов они повышались до 200 г, а при плавке в течение пяти с половиной часов до 400 г. По окончании плавки тигель оставляли в печи до полного остывания. Затем отбивали крышку тигля, высыпали остатки графита, а шлак разбивали. Металл извлекался из тигля в форме «сплавка, имеющего вид хлебца» и при медленном охлаждении постепенно затвердевал.
Поверхность застывшего металла получалась либо ровной, либо с некоторым углублением около середины, «в котором кристаллы булата более видимы и между собой перепутаны». «Это,— говорил Аносов,— составляет усадку». Она была сильнее для более твердой стали. Отсутствие усадки свидетельствовало о том, что «усадочная раковина находится внутри», и показывало, что «такой булат скорее остывает снаружи, нежели внутри». Подобные слитки не ковались и давали плохой сорт булата. Такое совершенно правильное толкование явления усадки, насколько нам известно, было впервые отмечено также Аносовым.
От длительности плавки зависел характер рисунка стали. После плавки в течение трех с половиной часов металл имел слабые продольные узоры, светлый грунт. После плавки в течение четырех с половиной часов узоры на металле получались волнистые, средней величины. Наконец, после плавки в течение пяти с половиной часов, при хорошем качестве графита, металл выходил с крупными узорами,— се тчатыми, «а иногда и с коленами». Все это подтверждало точку зрения Аносова о влиянии углерода на характер и ясность рисунка.
«Наибольшее время плавки и медленное охлаждение тигля» служили гарантией качества стали.
Шихтовка описана Аносовым в «Журнале опытам по приготовлению литой стали и булатов с краткими замечаниями».
Вот два примера шихтовки, взятые из этого журнала (табл. 1 и 2):
Таблица 1
Фиг. 13. Первая страница «Журнала опытам го приготовлению литой стали и булатов» П. П. Аносова.
Ковка105. Ковка производилась тюд хвостовым молотом, весом в два с половиной пуда (40 кг). «Сплавок нагревался в горне досветлокрасного каления и укладывался под молот широким основанием. Проковка велась при слабом обжатии при поворотах «кругом в одну сторону». Промежуточные нагревы проводились пять-девять раз.
Чем медленнее проковывался булат, тем лучше было его качество. После ковки металл разрубали. Разрубленные части снова проковывались под молотом сначала в бруски, а затем в полосы. Лучшие булаты, несмотря на твердость, проковывались из брусков в полосы с двух нагревов.
При ковке тщательно соблюдалась температура нагрева, та «степень жара», при которой «узор не теряется». Сталь нельзя было перегреть. «Потеря узора во время ковки — есть порча металла».
Полосы имели неровности и плены, обтачивались и клеймились для обозначения нижней части, которая шла на изготовление лезвий. Чистовая ковка проводилась при малом нагреве не сильнее «мяснокрасного цвета».
Закалка106. Операция нагрева и быстрого охлаждения стали называлась закалкой. Закаленная сталь обладала высокой твердостью, но вместе с тем и хрупкостью, «подобною стеклу». Для понижения хрупкости и для «сохранения, по возможности, твердости, приобретенной закалкой,— указывал Аносов,— искусство нашло средство в нагревании закаленной стали, но гораздо слабейшем, нежели при закалке». Далее он писал: «Предназначение изделия определяет меру нагревания, а появляющиеся на металле цветы (цветы побежалости) служат признаками для определения самой меры. Нагревание закаленной стали называется отпуском и главнейшие степени его по цветам суть: желтый, фиолетовый, синий и зеленый. Желтый цвет означает самую малую, а зеленый самую большую степень отпуска, при которой упругость металла начинает теряться».
Эти высказывания Аносова показывают, что он совершенно правильно определял понятие закалки и отпуска стали; также правильно характеризовал он свойства, изменяющиеся при отпуске.
Булаты закаливались в зависимости от назначения или в сале, или в воде, причем «самые твердые из них преимущественно в сале».
Аносов считал, что «оружие всякого рода достаточно закаливать в сале, «предварительно нагретом почти до точки кипения, ибо дознано из опытов, что в горячем сале закалка бывает тверже, в сем случае сало скорее ее охлаждает».
Таким образом, Аносов впервые дал метод закалки в «горячей среде» и объяснил ее действие.
Булаты закаливались путем нагрева откованного лезвия «докрасна» с последующим погружением в сало. После остывания лезвие обтиралось и для удобства наблюдения за цветами побежалости при отпуске зачищалось точильным камнем. Отпуск требовал большого искусства, так как нагрев производился «над углями» и при отпуске сабельного клинка различные части отпускались по-разному: у ручки — до зеленого цвета, у конца — до синего, в середине — до фиолетового, на месте «удара у лезвия» — до желтого. Отпущенный клинок .правился молотом и охлаждался в воде. Если же был необходим более упругий клинок, отпуск всего изделия проводился до синего цвета.
Аносов указывал также на возможность воздушной закалки тонких изделий «в быстрой струе воздуха».
Прсле закалки клинки подвергались точке и полировке. И для этой, казалось бы, простой операции Аносов дал ряд указаний, направленных на сохранение твердости. Он указывал, в частности, на недопустимость применения сухих точил, точение на которых вызывало нагрев и приводило к потере упругости; рекомендовал применять мокрые точила с соблюдением необходимых предосторожностей.
Впервые в истории металловедения Аносов описал и правильно объяснил также явление прижога закаленной стали при шлифовании.
Травление — «вытравка». Операция травления была необходима для выявления рисунка и определения качества булата. При разработке методов травления Аносов показал разное действие отдельных кислот.
Понятие о макроструктуре, как о показателе качества металла, выявление макроструктуры травлением, равно как и применение микроскопа для изучения макроструктуры как метода исследования, впервые были введены и Распространены Аносовым. Это — огромный вклад Аносова в металловедение.
Аносов дал также ясное описание строения стали, узоры которой похожи на виноградные гроздья, иногда расположенные рядами, сходные между собой. Правда, он не дал понятия о дендритах, позднее введенного Д. К. Черновым, но он наблюдал их, и его «виноградные грозды» дают точное описание дендритного (древовидного) строения стали. Этим он в известной мере предвосхитил дендритную теорию Д. К. Чернова.
К сожалению, до наших дней не сохранилось документального материала о макроструктурах сталей Аносова. Представление о макроструктуре и микроструктуре булатной стали дают фотографии начала нашего столетия, сделанные последователями Аносова (фиг. 14—15).
Первый клинок из -булатной стали был изготовлен Аносовым в 1837 г.109. Но об открытии Аносова еще долго не знали ни в России, ни заграницей. При состоянии связи того времени сведения с далекого Урала с трудом доходили до общественности столиц, а правительственные круги, преклонявшиеся перед английской литой сталью, которым было известно о блестящем успехе Аносова, его замалчивали. Не удивительно поэтому, что в то время, когда на одном конце России — на Урале секрета булата не стало, на другом — в Грузии попреж-нему считали искусство булатной стали тайной. Тайна закалки булата еще в 1838 г. служила средством для поэтических образов великому русскому поэту М. Ю. Лермонтову. Будучи в это время в ссылке на Кавказе, он посвятил булату известные стихотворные строки:
«Отделкой золотой блистает мой кинжал; Клинок надежный, без порока; Булат его хранит таинственный закал — Наследье бранное Востока
Сам Аносов, проводивший свои опыты с булатной сталью с исключительной научной тщательностью и с такой же тщательностью обобщавший их, не мог скоро подытожить их результаты.
На это у него ушло четыре года. И только в 1841 г., с появлением в печати его труда «О булатах», передовая общественность России широко заговорила об его открытии. «Сочинение Аносова «О булатах» возбудило общее внимание» — писала в июле 1841 г. газета «Мануфактурные и горнозаводские известия»
В октябре того же года «Горный журнал» заявлял: «Открытие способа приготовления булата, не уступающего качествами лучшим булатам азиатским, принадлежит, бесспорно, к числу важнейших открытий, которыми обогатилась наша промышленность в последние годы, и мы этим обязаны трудам Корпуса горных инженеров г.-м. Аносова.
Превосходные качества изделий, приготовленных из златоустовского булата, при необыкновенной дешевизне их, ручаются за прочность открытия».
Изделия, изготовляемые из булатной стали Аносова, отличались высоким качеством. С ними не могли соперничать изделия, изготовленные из любой стали, известной в то время. Например, «шпажный клинок из хорошего булата, правильно выточенный и соответственно закаленный, как оказалось по моим опытам,— говорил сам Аносов,— не может быть при гнутье ни сломан, ни согнут до такой степени, чтобы потерять упругость; при обыкновенном гнутье он выскакивает и сохраняет прежний вид; при усиленном (например, будучи загнут под прямым углом) не сломается и, будучи выпрямлен, не потеряет прежней упругости.
При этой связи в частях булатный клинок может быть тверже всякого другого, приготовленного из стали. Это и есть, без сомнения, предел совершенства в упругости, которая в стали не встречается»112.
Отмечая качества аносовской булатной пластинки, «Горный журнал» свидетельствовал: «она сгибалась без малейшего повреждения, издавала чистый и высокий звон. Отполированный и закаленный конец ее крошил лучшие английские зубила, тогда как отпущенный конец легко принимал впечатления и отсекался чисто и ровно».
Изделия из булатной стали демонстрировались на отечественных и зарубежных промышленных выставках и везде вызывали общее восхищение.
Обозреватели 3-й Московской мануфактурной выставки 1843 г. писали: «теперь Россия представляет единственный в целом мире источник нового булата лучших качеств. Булаты наши ценятся между азиатцами по крайней мере в десять раз дороже против здешней (-московской И. Б.) цены их. Сталь златоустовских заводов известна по отличному качеству вырабатываемого из нее белого оружия… Должно отдать справедливость их булатным кинжалам, которые оказались отличнейшего достоинства».
Иностранцы, поставленные Аносовым перед фактом, вынуждены были признать высокое качество его булатной стали, несмотря на свое скептическое отношение к русской промышленности. Рецензент английской газеты «Морнинг пост», обозревавший русское отделение на Лондонской всемирной выставке 1851 г. в отчете, составленном в довольно сдержанном тоне, все же отмечал, что «замечательный успех этой отрасли русской промышленности (выделка булатной стали), без сомнения, относить можно высокому качеству употребляемой стали».
«Было бы несправедливо,— заявлял он при этом,— не воздать должной почести и хвалы усердию, энергии и знаниям того ученого Корпуса инженеров (речь шла о П. П. Аносове И. Б.), на который возложено великое призвание распространять ремесленность и промышленность… в глубине лесов Урала и Алтая»115.
И в то же время иностранцы на русской службе пытались принизить роль Аносова в сталелитейном деле.
По случаю открытия Аносова перед Российской Академией наук был поставлен вопрос о присуждении ему Демидовской премии. Его способ производства булатной стали был передан на заключение академикам-иноземцам (непременный секретарь Фус и др.).
Фиг. 17. Чертежи устройства печей П. II. Аносова для производства булата. Устройство печи (чертежи AB—план и разрез): а — топило; b — колосники; с — пролеты из топила под основанием свода; d—чугунный ящик; е —кирпичи, поставленные на ребро, на которые становился ящик; f —обратные пролеты, под ящиком; стены по сторонам ящика; х — свод; i—пролеты; выведенные с одной стороны до высоты свода, в которые обращалось из него пламя; h — дымовая труба.
Не признать высоких качеств аносовских булатов было нельзя — они были слишком очевидны и слава о булатах шла далеко. Поэтому иностранцы на русской службе постарались запутать дело. Дав в общем высокую оценку булатной стали, они решили поставить под сомнение способ ее производства, разработанный Аносовым.
В своем заключении эксперты заявляли: «Если бы в сочинении Аносова было указано, каким образом можно всегда с удачею изготовлять эту (булатную И. Б.) сталь, то не колеблясь должно было признать это открытие одним из полезнейших обогащений промышленности, и в особенности отечественной. Но в описании столь мало сказано о способе приготовления этого булата, что надобно думать, не представляет ли Аносов себе самому этой тайны, или может быть и ему самому только временем и случайно выдается изготовлять такую сталь
При таковом положении дела академики не решаются представить Академии о присуждении Аносову демидовской награды за изобретение, которое не содержалось еще общим достоянием и о котором даже неизвестно, основано ли оно на приемах верных и доступных для всех и каждого».
Вопреки истине, вопреки тому, что Аносов дал вполне ясное представление о своем способе в сочинении «О булатах»,— Академия отклонила предложение о присуждении ему премии. Такое позорное событие могло иметь место только в условиях крепостнической, а позднее и капиталистической России, где раболепие правящих классов и низкопоклонство «официальной» науки перед иностранщиной не знало границ.
Однако ни общие условия того времени, ни отдельные реакционные попытки не могли подорвать значения открытия Аносова. Начатое им прогрессивное дело, знаменовавшее новый этап в развитии металлургии, упорно прокладывало себе путь вперед усилиями самого Аносо-на, а после него его последователями.
К ОГЛАВЛЕНИЮ
www.himikatus.ru
Секреты булата. Загадка булатного узора
Секреты булата
После того как разработана технология получения булатных слитков, показаны приемы получения рисунков различных сортов узорчатой стали и оценены ее свойства, представляет интерес еще раз проанализировать данные, которые накопила история и наука о производстве этой замечательной стали, ее термической обработке и отделке.
Наши разработки теории и производства булата убедительно показали, что булатный узор и необыкновенные свойства этой стали являются следствием не только макро-, но и микронеоднородности металла. Если макронеоднородность зависит от физической неоднородности, обусловленной сохранением в объеме жидкой стальной ванны недорасплавленных частиц с небольшим содержанием углерода, то микронеоднородность возникает вследствие диффузии углерода из слоя в слой при нагревах изделий и тщательного «перемешивания» слоев металла во время пластической деформации.
Таким образом, с одной стороны, правильна расшифровка работ П. П. Аносова профессором А. П. Виноградовым; с другой — Д. К. Чернов, Н. И. Беляев и их последователи совершенно верно указывали на необычную микронеоднородность булата. В связи с этим экспериментально полученные А. П. Виноградовым узоры на образцах низкоуглеродистой стали являются только имитацией булата, поскольку в микроструктуре такой стали не наблюдаются выделения цементита (карбидов).
Очевидно, и наши разработки не могут претендовать на полное воспроизведение свойств булата, качество которого, как уже неоднократно указывалось, зависело от многих факторов: чистоты и состава исходных материалов, способов деформации и термической обработки, отделки, шлифовки и полировки готовых изделий.
В наше время хорошо известно: чистота и свойства железа и стали зависят не только от содержания в них таких вредных примесей, как кислород, сера и фосфор, но и от загрязненности металла неметаллическими включениями, представляющими собой главным образом мельчайшие частицы оксидов тугоплавких элементов. Применяемое нами мягкое железо, например, было получено путем окисления в жидкой стали ненужных примесей и перевода их в шлаковую фазу. Поэтому наше «чистое» по кремнию и марганцу железо обязательно содержало включения оксидов этих элементов.
В древние времена железо получали путем восстановления чистых по сере и фосфору руд древесным углем при температурах 800–1200 °C. При этих температурах кремний, марганец и многие другие элементы не восстанавливались, а их твердые оксиды растворялись в жидком шлаке. Железо в крице, очищенной от шлака, практически не содержало включений оксидов тугоплавких элементов. Таким образом, сыродутный и кричный процессы получения железа обеспечивали высокую чистоту металла не только по сере, фосфору и другим примесям, но и по неметаллическим включениям. Такое железо и приготовленные на его основе сталь и чугун могли обладать необыкновенной пластичностью и высокими механическими свойствами.
Есть еще одна возможная причина высокой пластичности и вязкости булатной стали. Недавно советским металлургом С. М. Барановым зарегистрировано открытие, связанное с «явлениями изменения структуры к свойств стали, обусловленных присутствием моноокиси кремния». Оказывается, наличие окиси кремния в сталях сильно снижает их пластичность и вязкость при низких температурах. Поэтому на заводе им. И. А. Лихачева, например, кузова автомобилей, предназначенных для северных районов, изготовляли из углеродистых сталей, отлитых методом бескремнистого раскисления. Эти стали обладают также повышенной коррозионной стойкостью в атмосферных условиях. С. М. Баранов считает, что при сыродутном способе получения железа и стали условий для образования моноокиси кремния не существовало, и поэтому булатные стали хорошо ковались при низких температурах, были прочными и пластичными.
Действительно, в большей части клинков из булата обнаружено очень мало кремния, а содержание фосфора высокое (0,8–0,25 %). Мы уже отмечали благоприятное действие фосфора на коррозионную стойкость стали в атмосферных условиях. С другой стороны, фосфор усиливает междендритную ликвацию углерода при кристаллизации стали и делает феррит более устойчивым. В связи с тем что растворимость фосфора в аустените — гораздо меньше, чем в феррите, при охлаждении стали ниже 1400 °C из пересыщенного фосфором аустенита выделяются не фосфиды, а возникают ферритные участки с более высоким содержанием этого элемента. Такие участки устойчивы при дальнейшем охлаждении стадии они становятся зародышами при образовании феррита при низких температурах. Последнее приводит к тому, что в микроструктуре стали появляется неоднородность в виде светлых полосок или пятен. Такая неоднородность была выявлена нами в прокатанной на лист низкоуглеродистой стали, содержащей 0,11 % фосфора. Таким образом, фосфор мог усиливать микронеоднородность булата.
Если тайны булатных узоров и природы структурной неоднородности булата больше не существует, то в технологии приготовления булатных изделий — их ковке, термообработке и отделке — есть еще много белых пятен.
Многие булаты по содержанию углерода ближе к чугуну, чем к стали, поэтому булат — сталь сверхуглеродистая. Длительное время считали, что ковать чугун и сверхуглеродистые стали нельзя, они хрупкие и рассыпаются под ударами молота. Между тем булат надо было не просто проковать, а проковать так, чтобы сталь приобрела мелкозернистую структуру.
Совершенно прав металлург А. Герчиков, который замечает, что острота и стойкость острия зависят от того, насколько мелки зерна основной твердой фазы стали. Современную сталь для режущего инструмента подвергают специальной ковке, чтобы измельчить зерно. У булата же зерно должно было быть чрезвычайно мелким. Правда, зерно булатной стали мелкое уже в слитке, поскольку твердые частицы включений обеспечивали объемную кристаллизацию жидкой стали и затрудняла рост дендритов. При ковке слитка зерно еще более измельчалось. Теперь мы знаем, что одна из причин мелкозернистости и высокой пластичности сплавов железа с высоким содержанием углерода — их особая чистота. А если ее нет?
В последнее время появились работы, показывающие, что при определенных температурах деформации сверхуглеродистая сталь, содержащая 1,2–2,0 % углерода, может обладать высокой пластичностью и по другим причинам. Главным условием высокой пластичности и даже сверхпластичности является не только дисперсность зерен, но и постоянство их размеров при температуре деформации. Последнее обеспечивается, если в стали образуются очень тонкие частицы цементита (карбидов железа).
Подготовка стали к сверхпластичному состоянию осуществляется сравнительно недавно вновь открытыми методами термомеханической обработки. Сталь нагревают немного выше температуры перлито-аустенитного превращения и выдерживают необходимое время для растворения всех карбидов в аустените. Затем ее непрерывно деформируют, одновременно охлаждая. Это приводит к сильному измельчению аустенита, образованию субзерен и созданию значительного количества рассеянных дислокации. Выпадающие из аустенита по мере его охлаждения тонкие частицы карбидов (цементита) оседают на дислокациях и субзернах.
При температуре 727 °C (см. рис. 2) аустенит начинает превращаться в феррито-цементитную смесь. Дальнейшая непрерывная деформация приводит к образованию сверхтонких зерен феррита с однородным распределением субмикронных частиц цементита. Именно такой материал и обладает сверхпластичностью при 600–650 °C. Так, например, сталь, содержащая 1,6 % углерода, при этих температурах удлиняется перед разрушением более чем на 1000 %. После охлаждения до комнатных температур эта сталь обладала примерно в 2 раза большей прочностью, чем малолегированные инструментальные стали, и не уступала им в пластичности!
Еще выше поднимаются свойства стали после закалки. Мартенсит сверхуглеродистой стали имеет твердость и прочность на излом при сжатии, соизмеримые с карбидом вольфрама — одного из самых прочных и твердых после алмаза материалов. Но карбид вольфрама имеет нулевую пластичность при сжатии, и поэтому разрушается хрупко, в то время как сталь до излома пластически деформируется почти на 10 % и разрушается вязко. Таким образом, высокоуглеродистые заэвтектоидные стали при должной термомеханической обработке могут обладать высокой твердостью, прочностью и достаточно большой вязкостью. Мы уже знаем, что эти качества позволяют затачивать лезвие клинка до необыкновенной остроты.
Высокодисперсные зерна феррита, полученные в результате термомеханической обработки высокоуглеродистых заэвтектоидных сталей, обладают необыкновенно высокой подвижностью атомов на своих границах. При 650–800 °C диффузия атомов железа на поверхность зерна проходит в миллион раз быстрее, чем в его основу. Такие свойства стали должны хорошо обеспечивать ее сварку в процессе ковки. О. Д. Щерби экспериментально показал возможность сравнительно быстрой диффузионной сварки высокоуглеродистой заэвтектоидной стали с мягким железом и низкоуглеродистыми сталями при 800 °C. Им получен слоистый материал, аналогичный сварочному булату (дамасская сталь).
Знаменательно, что не так давно советские ученые А. Бочвар, В. Давыдов и Л. Лушников показали: при определенных условиях обычный чугун также становится сверхпластичным. Оказывается, при определенной температуре и достаточно быстрой деформации опасные изломы и трещины в чугуне не образуются. Зарождавшиеся очаги разрушения быстро «затягиваются». Механизм «затягивания» микротрещин связывают с большой скоростью диффузии, которая достигается лишь тогда, когда зерна металла очень мелкие и имеют круглую форму. Эксперименты с мелкозернистым белым чугуном, содержащим углерода 3,5 %, свидетельствуют, что при 70 °C удлинение образцом достигало 150 %!
Использовали ли древние кузнецы термомеханическую обработку стали для получения ее высоких свойств? Установленные факты позволяют положительно ответить на этот вопрос. Известно, что дамасские оружейники построили между двумя высокими горами мастерскую и вывешивали на сильном ветре раскаленные докрасна после ковки клинки. Подобным образом закаливали сталь и в древней Грузии. Только что откованый горячий клинок кузнец передавал подручному, и тот, мчась верхом на разгоряченном коне, размахивал ям над головой. Эти способы закалки булата непосредственно после ковки в потоке ветра кажутся сегодня романтичными; между тем они как раз и являются своеобразными приемами термомеханической обработки стали.
Совмещение ковки, закалки и отпуска — закономерный прием в технологии производства изделий с мелкозернистой структурой, высокой твердостью и упругостью. Для получения высокой твердости стали ее отпуск после закалки должен быть как можно более низким — при температуре 150 °C. При таком отпуске нельзя получить высокой упругости. Отпуск же при 300 °C обеспечивает высокую упругость, но при этом резко снижается вязкость стали вследствие развития необратимой хрупкости. Более высокая температура отпуска стали повышает вязкость, но снижает упругость.
Благоприятное сочетание всех этих свойств — твердости, упругости и вязкости — может быть получено при определенном температуре отпуска, только после термомеханической обработки, подавляющей хрупкость. Поэтому клинок, закаленный после ковочного нагрева, непосредственно после ковки должен обладать максимально благоприятным сочетанием всех указанных свойств. Похоже на то, что в древности это знали…
Кузнецу мало было владеть достаточно сложными приемами ковки булата, он должен уметь нагреть сталь до строго определенной, оптимальной температуры и прекратить деформацию металла в нужный момент. Как читатель уже убедился, отклонения от заданной температуры отрицательно сказывались на строении стали и могли значительно ухудшить свойства клинка.
Древние кузнецы, конечно, не могли измерять температуру металла, они судили о ней по цветам каления и побежалости на его поверхности при нагреве. Острые глаза кузнецов различали целую гамму цветов нагретой стали. Вот она. Бело-матовый — 1250 °C, светло-желтый — 1200, желтый — 1100, светло-красный — 950, красный — 850, светло-вишневый — 800, вишнево-красный — 750, темно-вишнево-красный — 650, темно-красный — 600, слабосветящийся — 550, серый — 330, светло-синий — 320, темно-синий — 300, фиолетовый — 285, коричнево-красный — 265, темно-желтый — 220 °C.
Древние манускрипты повествуют, что в давние времена мастера перед ковкой и закалкой булата плотно завешивали окна и работали в полной темноте. Как теперь ясно, это отнюдь не таинственный обряд. В темноте натренированному глазу легче проследить гамму цветов раскаленного металла. И все-таки надо иметь большой навык, чтобы не ошибиться во всех этих цветах и оттенках; да и не каждому дано такое зрение. Поэтому мастера постоянно искали более совершенные и простые способы определения температуры.
Особенно точно надо было определять температуру при закалке и отпуске изделий. Изменение температуры нагрева под закалку на 10–20 °C может заметно изменить свойства стали. Еще более важно точно зафиксировать температуру при отпуске. Даже несколько градусов отклонения от необходимой температуры отпуска для стали данного состава приводит к значительному ухудшению ее упругости.
Случай, о котором я сейчас расскажу, произошел не так давно. Приближалось начало осенней охоты, и охотники приводили в порядок свои ружья. Особенно важно восстановить упругость пружины бойка. Для этого пружину следует закалить и, главное, правильно отпустить. Делать это лучше всех умел один старый мастер. И делал, но с одним условием: никто не должен наблюдать за его работой. Заперся как-то этот мастер в термичке после конца рабочей смены, принялся за работу. Но какой-то парень все-таки подсмотрел его секреты. Увидеть увидел, а понять ничего не смог. Нагрел мастер пружину в печи и начал к ней прикладывать какие-то палочки: то одну приложит, то другую. Прикладывал, прикладывал и вдруг резко бросил пружину в воду. После этих манипуляций пружина стала необыкновенно упругой. Не знал этот парень, что «волшебник» пользовался старинным способом определения температуры стали при отпуске по воспламенению различных сортов дерева…
А способ этот применяется в металлургии и поныне. Американский инженер Р. Акофф рассказывает, что совсем недавно, когда на одном из металлургических заводов начали устанавливать термопару для определения температуры футеровки электропечи, старый сталевар спросил: «А зачем вы это делаете, можно же гораздо проще!» Он разжевал табак, плюнул в печь и по времени его воспламенения достаточно точно определил температуру футеровки.
Закалку стали применяли с незапамятных времен. Ее знали мастера Древнего Египта за несколько веков до нашей эры. Знаменитые Лейденские папирусы, найденные в Фивских гробницах, содержат описание способов получения и закалки металлов, относящихся к III веку. Лезвия древнеримских мечей из сварочного булата были закалены на мартенсит. На некоторых клинках мартенситная структура чередовалась с трооститом, причем в отдельных местах выступал феррит. Последнее свидетельствует о небольшом, менее 0,8 %, содержании углерода в сварочном булате. Интересно также, что в средней части клинков закалки не обнаружено.
Мартенсит в структуре лезвий очень древних мечей находят не часто, поэтому вещественных доказательств применения в глубокой древности термообработки не так уж много. Это объясняется тем, что, с одной стороны, большинство найденного холодного оружия подвергалось действию огня, а с другой — за многие сотни лет мартенситная структура стали, полученная закалкой, могла превратиться в перлитные структуры отпуска.
Широко применяли термическую обработку стали в Киевской Руси. Из исследованных Б. А. Колчиным более 200 цельностальных или со стальными лезвиями древнерусских клинков и наконечников стрел термическую обработку сохранило более 90 % изделий.
Древние кузнецы эмпирически владели почти всеми тонкостями технологии закалки и отпуска стали. Они знали, что чем быстрее охладить сталь после нагрева под закалку, тем она тверже и износоустойчивей. В. Шекспир так описывает меч Отелло:
Был в комнате другой в запасе меч,
Он закален в ручье, как лед, холодном.
Температура воды и растворимые в ней соли оказывают большое влияние на скорость охлаждения. Поэтому в древности пользовались для закалки родниковой водой, водой из минеральных источников, росой и так далее. Температуру воды и место ее отбора держали в строгом секрете. Сохранилась легенда о том, как один подмастерье захотел узнать, при каком жаре идет закалка. Когда мастер опустил в воду раскаленный клинок, тот сунул в сосуд палец. Рука подмастерья, проявившего излишнее любопытство, была отрублена ретивым мастером.
О том, какое значение имела температура воды и растворимые в ней соли, свидетельствует случай, который произошел уже в наши дни. На заводе вдруг пошел повальный брак по механическим свойствам деталей после термообработки. Причину установили не сразу; оказалось, что кто-то в закалочной воде помыл руки с мылом…
В древности искали и умели находить среды, в которых сталь охлаждается быстрее, чем в простой воде. Вот как Теофил описывает закалку стали, которая режет «стекло и мягкие камни»: «Берут трехлетнего барана, привязывают его и в течение трех дней его не кормят. На четвертый день его кормят только папоротником. Спустя два дня такой кормежки его ставят на следующую ночь в бочонок с пробитыми снизу дырами. Под эти дыры ставят сосуд, в который собирается моча барана. Собранная таким образом за две-три ночи в достаточном количестве моча барана изымается, и в указанной моче закаливают инструмент».
Когда кузнецы научились получать стали с большим содержанием углерода, они обнаружили, что клинки, закаленные в холодной воде, легко ломаются от удара. Поэтому в Персии, например, начали закаливать холодное оружие в мокром холсте. Известен также метод закалки, при котором клинок до термической обработки обмазывался для тепловой изоляции толстым слоем особой глины с разными примесями. Состав удалялся только с лезвия, подлежащего закалке в воде. Образовавшейся при этом демаркационной линии в каждой мастерской придавали своеобразный оригинальный рисунок, по которому можно отличить мастера, изготовившего холодное оружие.
Древние кузнецы знали и способы предохранения металла от окисления в период нагрева под закалку. Кузнец брал бычьи рога, сжигал их на огне, в полученный пепел примешивал соли и посыпал этой смесью изделия, шепча заклинание. После этого изделия нагревались и закаливались в воде или сале. Если не говорить о заклинании, то все это, как ясно теперь, являлось необходимым условием безокислительного нагрева стали.
Чтобы обеспечить необходимые свойства лезвию и обуху, закаленные клинки нужно было уметь отпускать при разных температурах. Делалось это путем нагрева клинка над раскаленными углями. Так при отпуске сабельного клинка различные его части отпускались следующим образом: у ручки клинок нагревали до зеленого цвета, у конца — до синего, в середине — до фиолетового, а лезвие — до желтого.
Применялась в древности и химико-термическая обработка стали. Цементацию стали делали так. Изделия смазывали свиным салом, обматывали ремешками, нарезанными из козлиной кожи, обвязывали льняными нитками, покрывали слоем влажной глины, сушили и помещали в горн. Поверхность стали науглероживалась, становилась твердой после закалки в воде, в то время как сердцевина оставалась вязкой, пластичной.
Кто не читал о варварском способе закалки стали в теле человека? В Древней Сирии, повествует легенда, клинок нагревали до цвета вечерней зари и шесть раз вонзали в ягодицы молодого раба. Известны приемы подобной закалки стали охлаждением в теле свиньи, барана или теленка. Был ли смысл в этом страшном ритуале? Оказывается, как это ни крамольно звучит, был. Он связан с химико-термической обработкой стали, которая называется цианированием.
Под цианированием понимают процесс насыщения поверхности стали одновременно углеродом и азотом. По сравнению с цементированным цианированный слой обладает более высоким сопротивлением износу, немалой твердостью, хорошей устойчивостью против атмосферной коррозии.
Твердое цианирование — процесс, аналогичный цементации. Он состоит во взаимодействии стали при нагреве с цианистыми солями. Основным компонентом солей является группа (СN), которая снабжает поверхность стали углеродом и азотом одновременно. Таким образом, цианирование — это совмещенный процесс цементации и азотирования. Для цианирования применяют чаще всего желтую кровяную соль К4Fе(CN)6 (. Если посыпать такой солью поверхность детали и нагреть ее до температуры 500–600 °C, то в результате диффузии углерода и азота в тонкий поверхностный слой детали произойдет цианирование.
Но почему желтую соль К4Fе(СN)6 называют кровяной? Оказывается, потому что ее длительное время получали сплавлением обугленной животной крови с поташом и железом. Не исключено, что древние воины после битвы обмывали свои клинки водой и сушили на кострах. На клинках оставалась кровь, а в озерной воде часто бывает много растворенного поташа (К2СО3). Так, совершенно случайно в древности осуществляли цианирование стали. Между тем воины замечали, что после применения в сражениях поверхность их клинков становится твердой, износостойкой. Это и могло послужить основой «кровавого способа» термообработки холодного оружия.
После ковки и термической обработки клинки обтачивались на точильных камнях, шлифовались и полировались. Эта работа включала ряд технологических операций и тоже требовала навыков, опыта и знания целого ряда ремесленных секретов.
Черновая шлифовка осуществлялась обычно на небольшом широком камне. Клинок заворачивался в предохраняющую ткань, обнажался только участок который подвергался шлифовке. Затем ткань передвигалась, и шлифовался следующий участок. Чистовая шлифовка делалась мелкозернистыми камнями различных сортов: корундом, наждаком, песчаником и другими. Доводка производилась на 4–8 камнях, а лучших клинков — на 15. Сохранилась миниатюра XII века, изображающая процесс изготовления мечей. Точило укреплено на деревянной колоде, наполненной водой. Подмастерье крутит ручку точила, а мастер шлифует клинок.
После обработки на камне клинки шлифовались различными тканями. В Индии нередко мастер заканчивал полировку пальцами своей руки. Советский филолог Н. Р. Гусева, прожившая несколько лет в Индии, так описывает процесс полировки изделий, который согласно преданиям был в ходу у древних индийцев: «Полировка осуществлялась при помощи трех компонентов: песка, наждака и пальца. Так вот, пальцем день за днем, с утра до ночи, месяц за месяцем, год за годом, поколение за поколением. И получали идеальную гладкую поверхность…».
Необыкновенное умение и титанический труд требовались, чтобы изготовить булатный клинок. Один клинок делался не часы, не дни, не месяцы, а годы…
Теперь совершенно ясно, что секрет булата был не один — их было несколько. Первая группа секретов относится к особенностям технологии получения слитка булатной стали с присущей ему неравновесной структурой, физической и химической неоднородностью. Эти секреты теперь расшифрованы, получен булатный слиток.
Вторая группа секретов относится к искусству ковки и получению булатных узоров. Многие приемы ковки булата сегодня осмыслены и познаны, воспроизведены почти все известные булатные узоры. Но тут еще последнее слово не сказано, работы в этой области продолжаются.
Третья группа секретов касается чистоты исходных материалов, обеспечивавшей особый химический и фазовый состав углеродистой стали, вырабатываемой в древности. Эти секреты современная наука также постепенно раскрывает.
Четвертая группа секретов включает термическую и химико-термическую обработку стали. Многовековой опыт металлообрабатывающего ремесла позволил оружейникам найти оптимальные режимы термомеханической обработки, цементации, закалки и отпуска стали, которые они держали в секрете. За время, прошедшее с тех пор, термическая обработка стали превратилась в стройную науку. Пользуясь современными теоретическими и экспериментальными методами анализа, можно раскрыть многие секреты, касающиеся термообработки древнего булата.
Наконец, пятая группа секретов касается отделки булатного оружия. Здесь следует решительно признать: воспроизведение методов шлифовки и полировки древних клинков — дело для нас чрезвычайно трудное. Поэтому пока еще никому не удалось достичь легендарной упругости булатных клинков.
Исходя из секретов производства булатной стали сегодня можно достаточно убедительно ответить на вопрос: что такое булат? Но ответ этот будет не прост.
Булат — это углеродистая заэвтектоидная сталь. Булат не только углеродистая сталь, булат — сталь сверхуглеродистая, близкая по составу к чугуну. Булат не только сверхуглеродистая сталь, булат — сталь особо чистая, без посторонних примесей. И наконец, булат — высокоуглеродистая сталь, обладающая неравновесной структурой, с ярко выраженной макро- и микронеоднородностью. Булат — слоистая сталь. Очень твердые слои с высоким содержанием углерода чередуются в булате со слоями, мало насыщенными углеродом и поэтому пластичными. В процессе ковки все слои переплетаются, образуя характерный естественный рисунок. Булат — узорчатая сталь. Структура булата после применения специальных методов ковки, термомеханической обработки и отделки обеспечивает ему необычайно высокие механические свойства. Булат — сталь, обладающая одновременно высокой твердостью, прочностью, вязкостью и упругостью. Чередование мягких и очень твердых участков на лезвии клинка превращает его в микропилу и обеспечивает самозатачиваемость. Булат — сталь, обеспечивающая необычайную остроту лезвия клинка и его самозатачиваемость. Таким образом, в понятие «булат» вкладывается целый ряд характерных особенностей этой замечательной стали.
Поделитесь на страничкеСледующая глава >
tech.wikireading.ru
Загадки истории. Тайны булата | Тайны мира и человека
4 848
О булате — стали, из которой в давние времена изготавливали необыкновенное по своим качествам и красоте холодное оружие, все наверное, наслышаны и начитаны с юнных лет. И неудивительно: слава о булатной стали (ее еще называют «дамасской») ходит по белу свету более двух тысячелетий, будоража не только умы ученых и специалистов, так и не подобравшихся к окончательной разгадке тайны, связанной с процессом получения изделий из булата.
Журнал «В мире науки» даже сообщает, что «процесс изготовления дамасской стали по американскому праву считается открытием и может быть запатентован». И это, заметим, в. конце XX века! Века. демонстрирующего миру такие взлеты человеческой мысли, такие умопомрачительные открытия буквально во всех отраслях знания, что по сравнению с ними разгадка лежащей, казалось бы, на поверхности некой тайны булата — не ахти какое дело! ан нет, оказывается. И продолжают до сих пор авторы различных книг и статей о булате «удивлять» нас эпизодом встречи Ричарда Львиное Сердце с султаном Саладином, описанным в романе Вальтера Скотта «Талисман». Ричард одним махом рубит своим двуручным мечом стальное копье, а Саладин подбрасывает в воздух вуалевый платок и рассекает его саблей на две половинки. Другие легенды «берут еще круче»-платок подбрасывают, и он сам падает на булатное лезвие — результат тот же.
ЗА СЕМЬЮ ПЕЧАТЯМИ?
А уж сколько восхитительных слов сказано о поверхностных узорах — характерном отличии булатного клинка. Специалисты даже и сорта булата классифицируют (условно, конечно) в соответствии с линиями узора. Различают три сорта. К низшему относят сирийские (шам), египетские и турецкие (нейрис, баяз) булаты с мелким полосатым или струйчатым узором на сером или буром фоне. К среднему — персидские и индийские (гынды) со средним и крупным узором на черном фоне. К высшему — персидские и индийские булаты (хоросан, табан) с крупным сетчатым и коленчатым узором на темном фоне с золотистым отливом. А лучшим из лучших считается булат «кара-табан», что в переводе с персидского означает «черный блестящий». Но есть особо знаменитые булаты, узоры на которых удостоены оригинальных названий. Например, необычный вертикальный узор на персидской сабле, хранящейся в Метрополитен-музее, называется «лестница Магомета».
Узор — это результат искусной ковки высокоуглеродистой стали (1,2-2% углерода), каковой и является булат. А видимые узоры на лезвии холодного оружия образует сетка карбида железа (Fе3С), или цементита, выпадающего при медленном охлаждении из сплава железа с углеродом (аустенита). При ковке эта сетка разрушается, и после протравливания и полировки на лезвии клинка появляется соответствующий узор. Не совсем, правда, ясно вот что. Цементит обладает высокой твердостью, но при комнатной температуре становится очень хрупким из-за сетчатой структуры — именно она открывает пути для распространения трещин. Тем не менее металл в булатном оружии совсем не хрупок, даже наоборот — очень вязок. Понятно, что таким он становится после ковки, когда разрушается цементитная сетка. Значит, ковка клинков должна производиться при относительно низкой температуре, так как известно, что при высоких температурах цементит опять растворяется в аустените.
Специалисты предполагают, что булат ковали в диапазоне температур от 650°С до 850°С. Тогда спрашивается: почему же европейские кузнецы не могли выковать булатные клинки из заготовок индийской стали (так называемого «вутца», или «вуца»), специально для такого оружия и сваренной? Может, потому, что они привыкли иметь дело с низкоуглеродистыми сталями, у которых высока температура плавления? Может, они пытались ковать вутц, когда металл уже был частично расплавлен? Тогда, естественно, сталь станет хрупкой. Но опять вопрос: неужели у уважающих себя мастеров кузнечного дела после первой же неудачи опустились руки? И неужели никто из них не сделал ни одной попытки проковать сталь не при белом калении, а, скажем, при нагреве заготовки до красного цвета (это примерно 850°С) или темно-вишнево-красного (650°С)? Что-то не очень верится. Тогда в чем же дело?
Вопросы, вопросы…
Ответить на них еще в начале XIX века пытался известный естествоиспытатель Майкл Фарадей — не удалось. Начитавшись его статей, пробирный инспектор Парижского монетного двора Жан Бриан изготовил клинки из дамасской стали, но так и не дал объяснения, как же он это сделал. Выдающийся русский металлург П. П. Аносов, как известно, раскрыл было вековую тайну и даже начал изготавливать булат промышленным способом, но не описал с достаточной точностью и определенностью тонкости технологических процессов, и после него булатное производство в Златоусте заглохло. И даже когда в конце прошлого века исследователи изучили все фазовые превращения, происходящие в стали, установили их зависимость от количества содержащегося в ней углерода и температуры нагрева, полного научного объяснения этапов изготовления булатных изделий — их ковки, термообработки, отделки — так и нет до сих пор. Более того, сегодня сама фазовая диаграмма «железо — углерод» в булате изучена вдоль и поперек, природа структуры булатной стали хорошо известна, тайны булатных узоров уже не существует, а воз… извините, булат и ныне там…
Есть чему удивиться! Хотя, собственно говоря, разве загадка булата единственная, связанная вообще с металлами? Мы, к примеру, утверждаем, что и сегодня немыслимо получить алюминий без электролиза, а в Китае есть гробница полководца Чжоу-Чжу, умершего 17 веков назад, некоторые детали орнамента которой на 85% содержат алюминий. Как же его получили в III веке? Те же китайцы во II веке до н. э. изготавливали сплав никеля медью и цинком, из которого делали монеты, а никель как элемент был открыт в Европе только в середине XVIII века.
Знаем: Индия славилась искусством своих металлургов задолго до нашей эры, о современниках тоже можно сказать немало хороших слов, а вот надо же — ответить на вопрос, каким образом почти из чистого железа (99,72%) изготовлена знаменитая колонна в Дели, никто не в силах. Нет-нет, мы не умаляем заслуг сегодняшних металлургов — и стали, превосходящие по своим качествам булат, у нас давно есть, и значительно более чистое железо в лабораториях получено. Но как же не удивляться: колонна в Дели весит 6,5 т и сотворена она в IV веке!
Молибден был открыт в 1778 году. Понадобилось больше столетия, чтобы выделить его в чистом виде, а в старинные острейшие самурайские мечи, как выяснил тот же П. П. Аносов, для .придания им прочности металлурги Страны восходящего солнца добавляли не что иное, как… молибден.
Ацтеки еще в XV веке умели изготавливать зеркала из хорошо обработанной, отполированной платины. Но как они это делали, ведь температура плавления платины 1769°С, она сваривается и поддается ковке только при белом калении? Спрашивается: где ацтеки брали такую температуру?
И т. д. и т. п.
Да, но почему же мы, живущие в конце XX века, проникшие в святая святых материи — в атом, в ген, нашедшие непостижимые связи вещества, встаем все же в тупик перед мастерством, обыкновенным (а может, и не обыкновенным) мастерством наших пращуров? Может быть, к разгадке их «тайн» мы подходим не с того конца, ошибаясь в методике самого подхода? Вряд ли — труды П. П. Аносова убеждают, что он шел правильным путем. А может, над нами все-таки довлеет не только авторитет привычных нам металлургических технологий, но и сама их традиционность? Но ведь о металлах и том же булате мы сейчас наверняка знаем больше, чем знали древние мастера. Тогда что же?
В конце-то концов давайте поставим себя на место древнего индийского металлурга, который искал способ получения этого самого вутца, и дамасского кузнеца, который начал ковать самый первый клинок, и сравним, у кого из нас больше преимуществ. Мы видим булатную сталь и изделия из нее и знаем, чего хотим: сделать то же самое. Древний металлург эту сталь никогда в глаза не видел, он только желал получить ее такой, какой она была в его мечтах, представлениях. Мы знаем конец пути и, по идее, можем прийти к нему, прошагав сначала в обратную сторону, то есть отталкиваясь от искомого, дифференцируя его, дробя на процессы, исследуя их, ища оптимумы… А каким путем шел к искомому — неосязаемому, невидимому, всего лишь мечте — древний металлург? Перебирал варианты всех последовательных операций, да еще в разных режимах? Да сколько же времени ему для этого бы понадобилось? Допустим даже, что металлурги объединились в какое-то цеховое сообщество и договорились искать желаемое, распределив определенные пути поиска. Тогда один, овладевший искомым, должен был бы поделиться знанием со всеми. Не так ли? Допустим, что так — возможно, в среде металлургов это могло быть. Но кузнецы?! Многие исторические документы свидетельствуют, что свои-то приемы и найденные режимы термомеханической обработки, закалки и отпуска стального изделия они держали в строжайшем секрете. Да что там, даже место отбора воды и ее температура были тайной. А ведь нам известно, что температуры закалки и отпуска должны быть настолько оптимальны, что отклонение, скажем, температуры под закалку на 10-20° уже изменяет свойства стали. Еще важнее зафиксировать температуры при отпуске — ошибка в 2-3° уже ухудшает упругость стали определенного состава. У древних кузнецов не было инструментов для измерения температуры, значит, они делали это на глаз. И — получали такие результаты? Да, это приходится признать, как и то, что в древности кузнецы владели какими-то особыми приемами, о которых мы сегодня не имеем понятия.
Так вот главный вопрос: к изготовлению булатной стали и изделий из нее древние металлурги пришли случайно или нет? Действовали ли они целенаправленно или для них самих было неожиданным то, чего они добились? Мне лично в случайность что-то не верится. И если они действовали целенаправленно, то остается только восхищаться их знаниями, опытом и великой одержимостью настоящих созидателей.
Евгений КРЮЧНИКОВ
taynikrus.ru
Секрет дамасской стали | Мастерам и мастерицам
Почему дамасская сталь такая знаменитая.
Дамаск и булат часто путают. В древности высоко ценилась индийская сталь, которую можно было купить в Дамаске, ставшем центром оружейного производства в эпоху Александра Македонского. Однако происхождение стали на дамасском базаре зачастую было трудно выяснить, поэтому называли «дамаском» практически все приобретенное там оружие.
Историки металлурги различают «чистый дамаск» – старую индийскую литую узорчатую сталь, и «сварной дамаск» или новую «дамасскую сталь». «Чистый дамаск», который более известен под русским названием «булат», упругий и очень твердый материал. Заточенное лезвие булатного клинка может долго сохранять остроту.
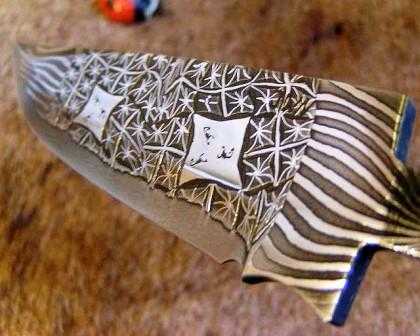
«Сварной дамаск» (современная дамасская сталь) или, как его еще называют, «сварной булат» уступает настоящему литому булату в твердости, но качество клинков из дамаска выше, чем из обычной стали. Способ получения дамасской стали изобрели случайно. Раньше оставшиеся отсечки, обрезки (металл ведь тогда был в дефиците, ничего не выбрасывали) – все собирали и варили сталь для ножей и инструментов. Однажды кто-то увидел, что получается красивый узор, да и качество металла становится заметно лучше, и стали складывать куски специально.
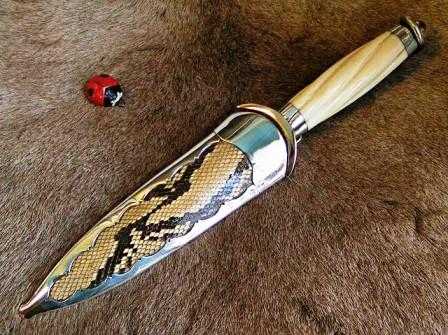
Известно, что само железо не обладает достаточной твердостью, она появляется в его сплавах с углеродом и легирующими добавками. В те времена углеродистой стали как таковой не было, но в зависимости от руды на молекулярном уровне исходный металл содержал какое-то количество хрома, молибдена или других элементов. В результате ковки сталь получалась лучше или хуже, но содержание углерода все равно оставалось недостаточным. Для улучшения свойств металла слои многократно перекладывали, нагревали на огне, закаливали, благодаря чему сталь приобрела необходимую прочность и твердость.
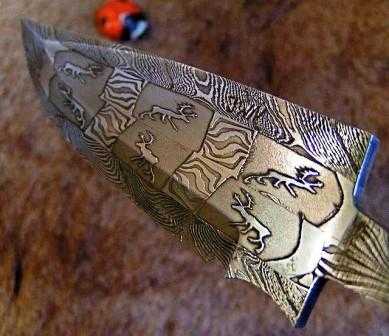
Сегодня кузнецы работают с готовым металлом. В современных марках сталей содержание углерода и легирующих элементов определено. Поэтому нет необходимости в некоторых трудоемких операциях. Но все-таки, если сравнивать старинную технологию и нашу – принцип остался тот же, только материалы разные.
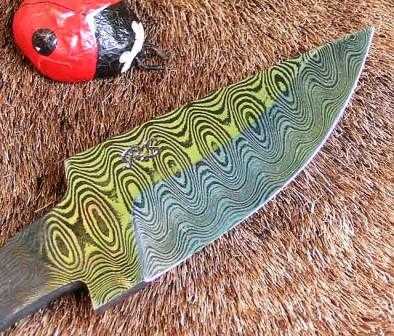
Рецепт булата только на первый взгляд прост: обмазывают тигель глиной, внутрь загружают куски разного металла, закрываю крышкой диаметром чуть больше, снова обмазываю глиной. Затем сверху наносится еще одна термостойкая обмазка. Тигель ставят в печь на 5,5-6 часов. Получается слиток – это и есть кристалл сверхтвердой структуры. Потом отрезают слитку «голову» и нижнюю часть и расковывают. На самом деле, все гораздо сложнее. Можно долго отливать, а потом окажется, что вышло с трещиной, и все старания напрасны.
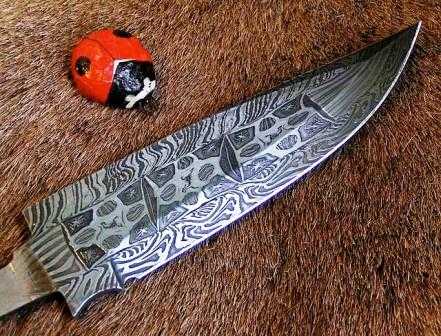
В изготовлении дамасской стали свои секреты. При изготовлении штемпельного дамаска уходит 1-1,5 часа на проковку и примерно столько же – на заготовку. В сложных дамасках – только 3-4 дня на то, чтобы собрать и сварить пакет. Мозаичный дамаск делают из слоев разной структуры – скрученной, слоистой, выложенной в определенном порядке. Скручивают в обычных тисках, в горячем состоянии.
Слои нужно тщательно складывать. По режущим свойствам мозаичный и штемпельный дамаск практически не отличаются, хотя цена у них разная.
Чтобы определить качество клинка, надо отдать его в работу. Если целый день резать что-нибудь твердое, клинок из дамаска сядет примерно до обеда, а из булата – где-нибудь к вечеру. И его тоже придется точить. В технике заточки свои секреты: можно заточить так, что клинок будет резать волос на лету.
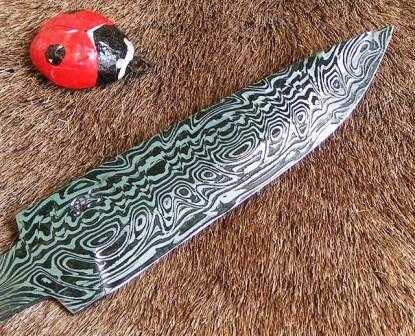
Задача кузнеца – сделать клинок, а оформить рукоять, ножны – как уже душа заказчика пожелает. Сейчас в почете красивые дорогие клинки – иметь такой у себя дома престижно. Но можно и веревкой обмотать ручку – это все равно будет нож – обычный рабочий, которым можно резать.
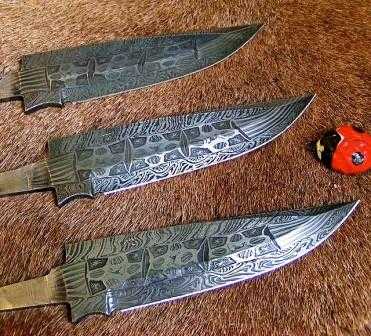
Обычно дорогие ножи не используют для работы: их показывают гостям, холят и лелеют. А на охоту, на рыбалку едут с простыми ножами без художественного оформления. Или, что еще хуже для клинка, – начнут бросать, демонстрируя его твердость выдержит он или нет. Так может и носик отколоться, а металл требует бережного отношения.
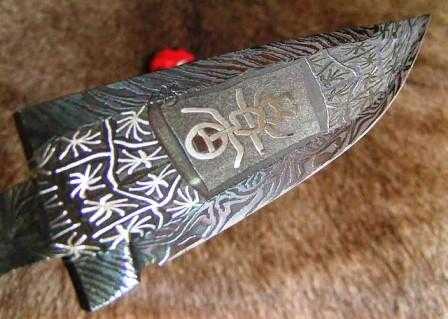
Кинжал или шашка должны всегда быть при мундире. Но оружие бывает парадно и боевое. Парадный клинок – напоказ – легкий и красивый, в серебре, золоте и даже бриллиантах. На бой шли совершенно с другим оружием. Боевой клинок обычно тяжелый.
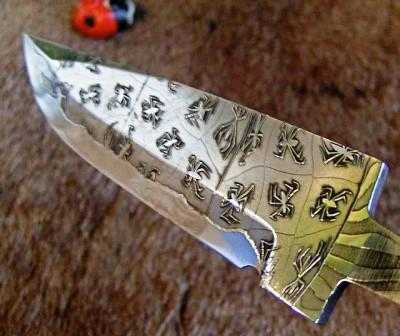
Существует в народе поверье: ножи дарить – не к добру. Но ведь оружие всегда преподносили в дар, и не только художественное, – «за храбрость и заслуги перед Отечеством», и даже «за вклад в торговлю» – перочинные и складные ножи. Сейчас добрые традиции возрождаются. И ценителей оружия становится все больше и больше. Поэтому, приступая к работе, хочется получить не только клинок с прекрасными режущими свойствами, но и показать всю красоту металла, вложить в него свою фантазию и уменье.
Пожалуй, весь секрет булата и дамасской стали – в работе.
podelki-shop.ru
Секреты изготовления дамасской стали. Мифы и реальность
Знаменитая дамасская сталь. Какими качествами обладали эти удивительные клинки? В чем секрет древней технологии? Дамаск для своего времени – это был революционный прорыв в создании высокопрочного металла и новой технологии. Легендарные мечи, рассекающие шелковый платок, имели необычайную остроту. А не миф ли это? Кузница двадцать первого века – царство традиционных технологий. Принцип создания авторских клинков не менялся столетиями. Основные элементы этого производства: открытый огонь, молот, наковальня, мастерство кузнеца. Примета нового времени в профессии кузнеца – исходные материалы. В старину ремесленники сами добывали руду, затем перерабатывали ее в металл. Современные кузнецы, как правило, оперируют сталью с легирующими добавками. Эти примеси и наделяют металл индивидуальными особенностями.
Превосходство дамасской стали над всеми другими сплавами – распространенный миф. Ученые считают, что это плод воображения писателей начала девятнадцатого века. В исторических романах того времени клинки Дамаска, обладали чудесными свойствами. Они рассекали кольчугу, как масло. Историки и металловеды опровергают эти легенды. Устоять против современных сталей, старинный дамаск вряд ли смог бы. Он, все-таки, был несколько проще по химическому составу и не так интересны были стали, которые в нем использовались. Тот «дамаск», который создают сегодняшние мастера, это, как правило, использование, уже, изначально высокопрочных сталей с хорошими характеристиками.
Тем не менее «дамаск» своего времени действительно отличался высокой прочностью и гибкостью. Это сочетание и делало мечи из дамасской стали превосходным оружием. Секрет – в особом сплаве.
В чистом виде, железо, очень мягкий металл, и не подходит для холодного оружия. Поэтому человек пользуется сплавами – соединениями железа с другими химическими элементами. Непременный компонент этих соединений – углерод. Он придает сплаву твердость. К примеру, в обычно гвозде, углерода находится сотые доли процента (0,06-0,16%) от всего металла. А в железнодорожном рельсе от 0,5 до 0,7%. Железные сплавы, содержащие меньше 2,14% углерода, называются сталью. После специальной термической обработки, она приобретает еще одно важное качество – упругость.
Главный секрет технологии производства «дамаска», многослойная заготовка, которая состоит из сплавов с разным содержанием углерода. Дамасская сталь – один из первых композитных, то есть, составных, материалов в истории. «Дамаск» — это сварочные технологии, сварка ковкой, когда идет диффузионное сближение слоев двух, трех или более, сталей, при высоких температурах, путем давления. Особую твердость «дамаску» придает основная часть пакета, которая состоит из сталей, богатых углеродом. Источник упругости будущего изделия – легирующие добавки и железо. Так, чередование слоев металла с очень высоким и очень низким содержанием углерода, придавало новому материалу: твердость, упругость и ударную вязкость (сопротивление ударным нагрузкам).
Следы этого коктейля в готовом клинке можно увидеть невооруженным взглядом. Характерный узор на лезвии «дамаска» оптический эффект неравномерного распределения углерода. «Дамаск» обладает своим неповторимым «лицом», своим рисунком, своей красотой в железе. Гомогенный материал ровный по раскрасу, не так интересен. Его, как правило, разрисовывают, либо растравливают, чтобы создать, какой-то образ.
Высокие качества конкретного клинка из дамасской стали закладываются на начальном этапе. Идеального рецепта создания «пакета» не существует. Подбор исходных материалов, их пропорции, принцип комбинирования, в древности, любой из элементов этого процесса, являлся секретом мастера, фундаментом превосходства его оружия.
Современный нож из дамасской стали – предмет гордости любого охотника. Благодаря технологии изготовления такой инструмент режет самые твердые природные материалы и ткани. Он хорошо держит заточку. Тем не менее, изделие этих мастеров редко используют по назначению. Основная функция их стальных произведений – декоративная.
sekach.ru
Учёные открывают тайну дамасской стали
Учёные открывают тайну дамасской стали
Оказывается, древние индийские ремесленники использовали нанотехнологии при изготовлении своих клинков из легендарной дамасской стали, но даже и не догадывались об этом…
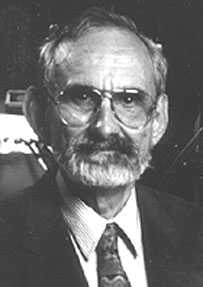
Robert Curl Jr
Легендарные клинки использовались (страшно подумать!) ещё в период с 1095 по 1270 гг. для того, чтобы запугать европейских оккупантов «священной земли» исламской цивилизации (в нынешней терминологии известных как «крестоносцы»).
Об этом рассказал лауреат Нобелевской премии по химии Robert Curl Jr, выступая перед зачарованной публикой во время 95-го Индийского научного конгресса в городе VISAKHAPATNAM: в частности, он рассказал, что, согласно современным данным, дамасская сталь изготовлялась мастерами на юге и в центре Индии ещё за 300 лет до н.э.
Самым забавным, – говорил он, – было то, что при изготовлении клинков древние мастера применяли методы нанотехнологии и даже не догадывались об этом. А древний булат всегда оставался острым и прочным, благодаря особой композиции углерода в структуре металла.
Сырьём для его изготовления была особая булатная сталь, называемая «вуц» (wootz steel), получаемая из специальной железной руды, которая как раз и добывалась в центральной и южной части древней Индии и Шри Ланки.
Сталь wootz получалась из этой руды и формовалась с помощью специальных тиглей, в которых она плавилась, выжигались примеси и добавлялись, говоря современным языком, необходимые присадки, включая большое количество углерода (до уровня примерно 1,5 % против 0,1%, которые добавлялись в обычное железо).
Curl Jr напомнил, что даже Tipu Sultan использовал меч из такой стали в битвах против британских войск в конце 18 века.
Писатель Walter Scott в своей книге «Талисман» описал сцену битвы между британским рыцарем Ричардом Львиное сердце и сарацином Saladin, происходившей в конце третьего Крестового похода (в октябре 1192 г.). И в то время как Ричард пользовался отличным британским мечом, блестящим, как солнце, у Саладина была кривая турецкая сабля тускло-голубоватого цвета, украшенная десятками миллионов извилистых линий…
Сэр Curl Jr пояснил, что эти «извилистые линии» были ничем иным, как мельчайшими углеродными наночастицами, которые и придавали такую прочность мечам из дамасской стали.
Удивительно, что по непонятным причинам секрет производства этой стали был надолго утерян: европейские мастера никогда и не пытались воспроизвести эти достижения, и даже мастера исламского мира утратили этот секрет где-то с середины 18-го века.
Однако в наши дни учёные разгадали секреты дамасской стали, и помогли им в этом методы современного материаловедения, методы нанотехнологий.
‘Nanotechnology was used by ancient Indians’
http://www.newindpress.com/NewsItems.asp?…
Дамасские клинки изготовлялись при помощи нанотехнологий
Открытие немецких ученых-кристаллографов из Дрезденского технического университета еще больше усложнило попытки раскрыть утраченную технологию изготовления знаменитых дамасских мечей, сообщает журнал National Geographic. Эти мечи ковались на Ближнем Востоке и в Индии с VIII в. и вплоть начала XVIII в. нашей эры из булатной стали, которую еще называют «вуц». Клинки славились своей исключительной прочностью, витиеватой структурой поверхности и небывалой остротой, однако технология их изготовления была утрачена. По легенде, такой клинок мог рассекать надвое упавший на острие лоскут шелка.
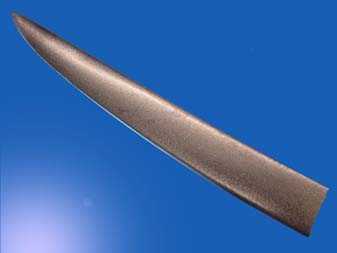
Дамасский клинок XVII века (National Geographic)
Изучив молекулярную структуру сабли XVII века под электронным микроскопом, немецкие кристаллографы обнаружили в лезвии углеродные нанотрубки и нановолокна из цементита (карбида железа). По мнению дрезденских исследователей, именно вкрапление этих сложных элементов и объясняет уникальные свойства дамасской стали. Нанотрубки, как оказалось, присутствуют в мягких слоях стали, которая отличается неоднородной структурой.
Ученые предполагают, что углеродные нонотрубки и нановолокна образовывались в клинках вследствие сложного процесса обжига и ковки. А как только клинки уже были практически готовы, кузнецы травили сталь кислотой, нанося на них неподражаемый и узнаваемый рисунок. Специалисты считают, что, поскольку углеродные нанотрубки устойчивы к действию кислоты, они защищали находящиеся внутри них нановолокна из более хрупкого цементита. После травления многие подобные наноструктуры выпирали из поверхности лезвия, придавая клинку сходство с пилой на наноуровне и, соответственно, необыкновенную остроту.
http://science.compulenta.ru/295375/?…
Отчет ученых из Германии раскрывает тайну дамасской стали
Несравненно острые, прекрасные и роскошные мечи и ножи из дамасской стали некогда были предметом роскоши у знатных людей Востока и Запада. К сожалению, вслед за тем, как в конце XVII в. ресурсы железа в главном месторождении, узбекских рудниках, иссякли, технология выплавки дамасской стали также канула в Лету. В XX веке специалисты, прибегая к современным средствам, пытались восстановить технологию дамасской стали, но тщетно.
Совсем недавно, наконец, нашлись ученые, утверждающие, что сделали это.
Как сообщило агентство Юнайтед Пресс Интернэшнл, отчет ученых из Германии раскрывает тайну дамасской стали. Вероятно, благодаря этому, современная обрабатывающая промышленность сможет возродить производство этого знаменитого материала.
В XVIII веке способ плавления дамасской стали был утрачен. Петер Пауфлер из Дрезденского технического университета (Германия) вместе со своими коллегами при помощи электронного микроскопа высокого разрешения подверг анализу саблю из дамасской стали XVII столетия.
Команда Пауфлера обнаружила, что микроскопическая структура дамасской стали указывает на то, что в процессе литья в нее, вероятно, добавлялись другие компоненты, и можно даже утверждать, что это представляет собой самое раннее применение технологии углеродной нанотрубки. С другой стороны эти компоненты способствовали образованию нанопроволок карбида железа, благодаря которым мечи из дамасской стали обладали особенной твердостью и привлекательным внешним видом. Результаты этого исследования были недавно опубликованы в журнале Nature.
http://nanoblog.ru/…sskoy-stali/
Дамасская сталь – древние нанотехнологии
Всем известны уникальные, почти сказочные свойства Дамасской стали. Иделия, сделанные из неё прочны и остры. Новейшие исследования в области нанотехнологий позволили выяснить, что при производстве Дамасской стали применялись углеродные нано-структуры, подобные современным
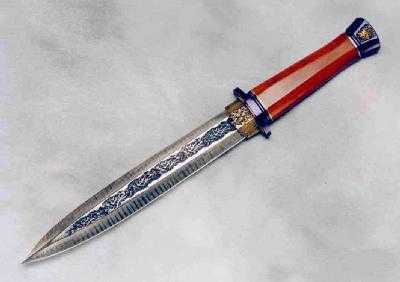
Кинжал «Крисис»
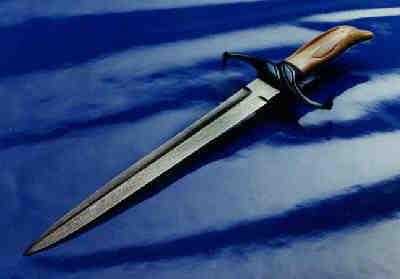
Кинжал «Дельфин»
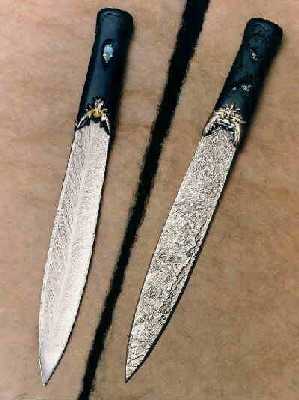
«Жизнь и Смерть». Классическое Дамасское лезвие слева и текстурированная сварочная сталь справа. Ручки кинжалов икрустированы золотом и серебром. На кинжале «Смерти» изображён золотой демон, а «Жизни» – серебрянная орхидея
Дамасские сабли и кинжалы изготавливались в X веке в Индии, где они также назывались «вуц».
Профессор Питер Пауфлер (Peter Paufler) из Технического университета Дрездена, провёл ряд исследований дамасских сабель. И сейчас с большой уверенностью может говорить, что при их производстве применялись нанотехнологии.
Peter Paufler
Чтобы это выяснить, кусочек вуца был растворён в соляной кислоте. Результат реакции был заснят Пауфлером c помощью электронного микроскопа. Анализ снимков показал схожесть структуры дамасской стали с современными углеродными нанотрубками, используемыми для увеличения прочности металлов.
(Углеродные нанотрубки – протяженные цилиндрические структуры диаметром от одного до нескольких десятков нанометров и длиной до нескольких микрон. Состоят из нескольких свёрнутых в трубку гексагональных графенов и заканчивающихся полусферической головкой).
В составе вуца есть железо и примесь карбида железа, который содержится в виде нанонитей. До исследований Пауфлера было не до конца понятна природа их возникновения. По его предположению, этот эффект возникает именно за счёт использования нанотрубок.
Некоторые примеси в стали при высокой температуре вызывали рост углеродных нанотрубок. (Углерод в вуц попадал как продукт горения дерева и листьев в печи при плавке стали). Созданные трубки наполнялись карбидом железа. Так и возникали эти тончайшие нити.
Очевидно, что в древности люди и не знали, что используют именно нанотрубки и не до конца понимали их природу, но совершенно очевидно, что они обладали технологией их производства.
В данный момент профессор Пауфлер работает над выяснением деталей этой древней технологии. Ведь совершенно очевидно, что она значительно проще и совершеннее сложной технологии современного производства таких материалов.
В наше время, первое упоминание о наблюдении волокон диаметром порядка 100 нм, полученных при термической обработке окиси углерода и железа были опубликованы в статье советских учёных Радушкевича и Лушкиновича в 1952 году. Первый общеизвестный факт наблюдения нанотрубок приходится на 1991 год (исследователь Ииджима), а в 1996 году группа Смоли, Крото и Кёрла была удостоина нобелевской премии за исследования в этой области.
http://tonos.ru/…les/damascus
История не столь уж новая, но всегда интересная… Тем более, что многие об этом ещё и не слышали. Поражает, как солидный учёный, лауреат Нобелевской премии по химии (1996) Robert Curl Jr так просто рассказывает эту историю своим индийским коллегам. Никакой заумной «химии», зато откровенный энтузиазм и восхищение научными достижениями древних мастеров, напоминание индийцам о славном прошлом их далёких предков и земляков… Вот как надо выступать перед аудиторией! Ну, а потом идут просто научно-популярные очерки, в которых уже подробно и последовательно рассказывается о поиске и открытии секретов славной дамасской стали… Да, древние мастера, доживи они до наших дней, могли бы чем гордиться. И ещё. Говорят, что и наши уральские умельцы ещё в позапрошлом веке владели секретами получения дамасской стали (булата). Подробностей сейчас не помню, а, вроде бы, они ковали раскалённую добела заготовку клинка и при этом постоянно посыпали её порошком из древесного угля…
www.nanonewsnet.ru